フレキシブル基板(FPC)の設計にはリジッド基板ともまた違ったコツがあります。
前回の記事「パターン設計編」ではP-Flex®️のパターンを設計する際のコツについて紹介しました。
この記事ではその他のレイヤー、レジスト・シンボル・外形のコツを紹介します。
基板のレイヤーの種類については下記記事をご覧ください。
▶ フレキシブル基板 の用語解説【初心者向け】フレキシブル基板
レジスト設計のコツ
パターンに被せる
レジストを設計する際には、パターンとレジストを固定することに注意して設計をします。
パターンは通常レジストの下にあるため、レジストに押さえられている状態です。一方、開口部ではそうではないため、パターンを一回り大きくすることでレジストを被せることが推奨されます。P-Flex®️はソルダーレジストを印刷しているため、フィルムカバーレイと比較すると機械的に押さえる力は弱くなりますが、それでもある程度の効果は期待されます。
パッド
浮きを防ぐにはできるだけ大きくレジストを被せる方が良いので、図の一番左の例のようにパッドの全周にレジストを被せる方法が最も有効です。その他にも、スペースの都合によっては一部だけをレジストに被せる他の設計もあります。
ただし高周波回路を設計している場合は、尖ったパターンを設計するとその部分がアンテナとして機能してしまうので気をつける必要があります。
表面実装部品用パッド
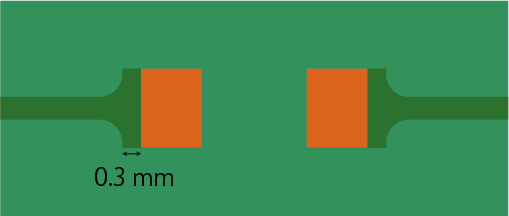
表面実装部品の開口部には、単に長方形を利用します。丸いパッドと同様に、0.3 mmほど配線方向にレジストを被せることで強度を増します。
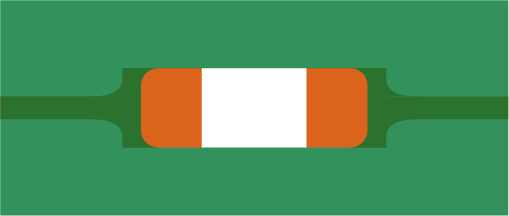
通常フィルムカバーレイを利用する場合は裂けを防ぐために角を丸くしますが、P-Flex®️ではソルダーレジストを印刷しているため裂ける心配はなく、角を丸くする必要はありません。
またフィルムカバーレイの場合は細かい穴開けが難しく、上図のように端子間も穴開けをすることがありますが、ソルダーレジストは細かいパターンも得意なため端子間にレジストを印刷できます。
シンボル設計のコツ
折り曲げ線
必ずしも必要ではありませんが、折り曲げ線を目安として入れておくと便利です。
パターン編に書いた通り、線幅が変化する部分等は屈曲部より1 mm離すことが望ましいです。また、折り曲げ線はパターンに描く方法もあります。
外形設計のコツ
外形の設計はリジッド基板とフレキシブル基板で最も異なる点ではないでしょうか。
フレキシブル基板(FPC)の設計ではフィルム(基材)が裂けないようにすることがポイントです。パターンの設計のコツと同様に、特に屈曲時に力が集中するような部位を作らないように気をつける必要があります。
角を丸くする
凹の角は丸くします。パターン編でも「コーナーを曲線で設計する」というコツがありましたが、それと同じ理由で凹の角は屈曲時に裂けやすいためです。
▶ フレキシブル基板 P-Flex®️ 設計のコツ「パターン設計編」
スリット止め
スリットは角と同様に裂けやすい部分です。ここを裂けにくくするためにスリットの終端を丸くします。
コーナー溝
角を裂けにくくするための方法として、丸くする以外に溝を設ける方法もあります。この場合、スリット止めと同様に溝の終端を丸くします。
補強帯
これは正確にはパターンの設計ですが、基材を補強する方法の一つなので外形のコツと合わせて紹介します。
角やスリットなど基材の裂けやすい部分の内側にパターンを配置することで、最悪裂けてしまった場合でも裂け目が広がることを防げます。しかしこれは最悪の事態を防ぐ方法なので、やはり裂けないような設計をすることが一番重要です。
まとめ
パターンと同様に、レジスト・シンボル・外形にもそれぞれ特有のコツがあります。特に外形のコツはフレキシブル基板(FPC)に特有なので、リジッド基板の経験しかない方は注意して設計すると耐久性の高い基板が設計できると思います。
関連記事
本文中にも書きましたが、パターンの設計については以前の記事をご覧ください。また、この記事で参考にした文献もそちらに載っています。