Environmental results
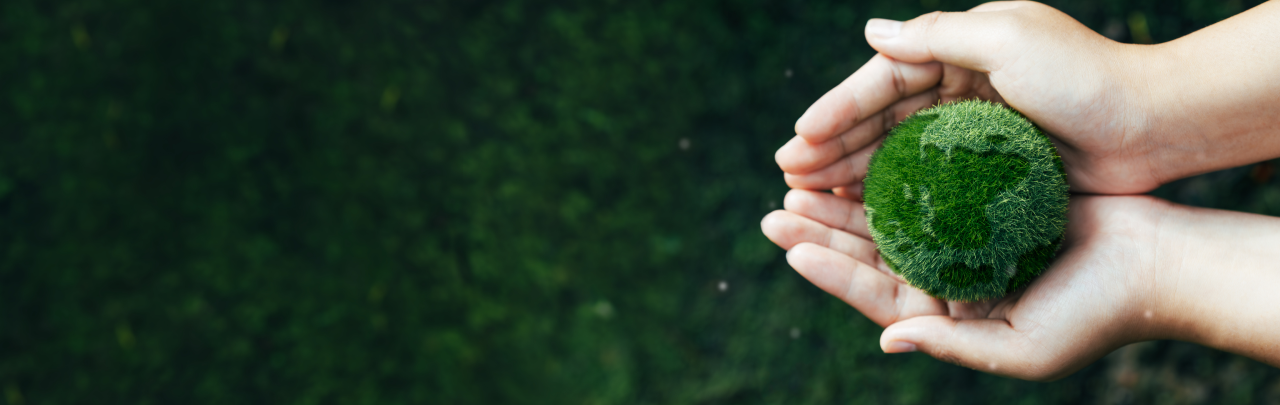
Environmental data: Our contribution to a more sustainable society
Amidst escalating efforts to cut greenhouse gas emissions, we’re currently seeing a global trend toward minimizing environmental impact.
In January 2022, the California Senate passed a law requiring all companies with annual revenue of more than $1 billion US dollars (approximately 115 billion Japanese yen) to disclose all emissions each year. These new disclosure requirements apply to direct emissions (Scope 1), emissions from purchase and use of electricity (Scope 2), and indirect emissions, including emissions from the company supply chain (Scope 3).*1 In Japan, the government revised the Corporate Governance Code, making it mandatory for companies listed on the Tokyo Stock Exchange's Prime Market, the top tier newly established in April 2022, to disclose information in accordance with the recommendations of the Task Force on Climate-related Financial Disclosures (TCFD).*2 At Elephantech, we believe that it’s one of our responsibilities as a company to actively disclose our environmental data and we created the following infographic to visualize how we are reducing our environmental impact from the perspectives of resource usage, carbon dioxide emissions, and water consumption.
At Elephantech, we have made it our mission to “make the world sustainable with new manufacturing technologies” and will continue to work to reduce our own environmental footprint so as to contribute to a more sustainable electronics industry.
- *1California senate passes Bill for first Law in US requiring companies to disclose all GHG Emissions
- *2IFRS Foundation announces International Sustainability Standards Board, consolidation with CDSB and VRF, and publication of prototype disclosure requirements
Our environmental data
Extraordinary savings in resources and energy
The above estimate assumes the following conditions:
All calculations are based on a substrate surface area of 1 m2
Copper consumption
Based on estimation for a single-layer flex circuit (18 µm copper layer, 30% surface coverage)
CO2 emissions and water consumption
Based on estimation for a double-layer flex circuit (25 µm polyimide film, 6.6 µm copper with 30% surface coverage, 0.1 µm gold with 10% surface coverage).
Different board designs also achieve a carbon footprint reduction of between 70-80%.
Production costs
Comparison of the estimated cost of large-scale mass production contracts.
Using metal inkjet printing technology to dramatically reduce environmental impact while retaining exceptional product quality.
Conventional PCB production process (subtractive manufacturing)
- Subtractive manufacturing is the mainstream method for producing electronic components and has been in use for more than a hundred years.
- However, a major drawback of this method is its significant environmental footprint—covering the entire substrate in copper foil and then etching away the unnecessary metal not only wastes resources, it produces a large amount of toxic waste water.
Elephantech Pure Additive™ production process
- Metal is nanoized into ink and printed directly on the substrate only where required.
- The production process ensures minimal environmental impact: Less wastewater, less water consumption, and less carbon dioxide emissions.
- Although an extremely difficult technology to develop, we are proud to say we are the first and only company in history*1 to have successfully mass produced and commercialized products using metal inkjet printing.
- *1Statement based on publicly available information as of January 2022
Climate change: Our CO2 emissions results
- We used life cycle assessment (LCA) to compare the lifetime carbon dioxide emissions of printed circuit boards made using our Pure Additive™ method with those made using conventional production processes.*1 The following results are based on in-house analysis and calculations that have been verified by a third party.
- Numbers shown for conventional printed circuit boards were taken from research published by the Hong Kong Polytechnic University.*2 Their study, “Carbon Footprint Analysis of printed Circuit Boards,” .presents detailed life cycle assessment based on actual data from Shenzhen Sunshine Circuit Technology, Co., Ltd., and our calculations are based on the same results disclosed in this study.
- *1Assumptions: Copper film thickness 6.6um
- *2Winco K.C. Yung, Subramanian Senthilkannan Muthu, Karpagam Subramanian, Chapter 13 - Carbon Footprint Analysis of Printed Circuit Board, Editor(s): Subramanian Senthilkannan Muthu, Environmental Carbon Footprints, Butterworth-Heinemann, 2018, Pages 365-431, ISBN 9780128128497, https://doi.org/10.1016/B978-0-12-812849-7.00013-1.
Carbon dioxide emission results for production
Unit: kg-CO2eq/m2
Item | Existing
2 layers |
ELT method
2 layers, 6.6um |
Estimation logic | Simulation logic |
---|---|---|---|---|
Materials - CCL | 15.9 | 0.2 | 25µm polyimide film | Proportional to the number of layers |
Materials - DES | 9.1 | 0.0 | No DES process | No change |
Materials - Electroless Copper Plating |
0.3 | 1.2 | From existing, assuming proportional to copper thickness. Assume 0.5µm copper thickness for existing method. 0.3*6.6/0.5 0.3*6.6/0.5 |
Proportional to the number of layers and copper thickness |
Materials - Gold Plating |
7.5 | 7.5 | Same as existing | No change |
Materials - Other | 6.6 | 2.4 | Removes materials needed for subtractive process, adds metal ink and other necessary materials |
No change |
Materials - Waste process |
9.4 | 0.5 | 1/20 of existing, given the waste amount is estimated as 1/20 |
Proportional to the number of layers and copper thickness |
Production energy | 37.1 | 10.9 | Simulation of actual data | Proportional to the total material carbon footprint |
Transportation&Packaging -Materials | 17.0 | 1.8 | From existing, assuming proportional to the total material carbon footprint |
Proportional to the total material carbon footprint |
Waste management | 0.8 | 0.0 | 1/20 of existing, given the waste amount is estimated as 1/20 |
Proportional to the number of layers and copper thickness |
Total | 103.8 | 24.5 |
Water Consumption Reduction Benefits
Conventional manufacturing method
Major item | Process | Waste liquid |
---|---|---|
Start material | CCL(Film+Cu) | Omit the waste liquid in CCL production |
Drilling process | Via hole drilling | |
Washing | Waste water | |
Catalyst addition | Cleaner | Alkali waste liquid |
Washing | Alkali waste liquid(weak) | |
Soft Etching | Heavy-metal acid waste liquid (contains Cu) | |
Washing | Acid waste liquid(weak) | |
Predip | Acid waste liquid | |
Add palladium catalyst | Acid waste liquid, Recovery | |
Washing | Acid waste liquid(weak) | |
Electroless Cu | Accelerator | Sn, Acid waste liquid (Pd contain) |
Washing | Acid waste liquid(weak) | |
Electroless Cu | Heavy-metal acid waste liquid (contains Cu) | |
Washing | Alkali waste liquid(weak) | |
Drying | ||
Electrolytic Cu | Cleaner | Acid waste liquid |
Washing | Acid waste liquid(weak) | |
Predip | Acid waste liquid | |
Electrolytic Cu | *None since it is circulated | |
Washing | Acid waste liquid(Cu contain) | |
Rust prevention | Alkali waste liquid(weak) | |
Washing | Alkali waste liquid(weak) | |
Drying | ||
DF | Soft Etching | Acid waste liquid(Cu contain) |
Washing | Acid waste liquid(weak) | |
Drying | ||
DF laminate | ||
Exposure | Exposure | |
DES | Developing | DFR, Alkali waste liquid |
Washing | Alkali waste liquid(weak) | |
Etching | Acid waste liquid, Recovery | |
Washing | Acid waste liquid(weak) | |
Stripping | DFR, Alkali waste liquid | |
Washing | Alkali waste liquid(weak) | |
Drying |
Elephantech's manufacturing method
Major item | Process | Waste liquid |
---|---|---|
Start material | Film | |
Drilling process | Via hole drilling | |
Printing | Printing | |
Drying | ||
Sintering | ||
Cleaner | Alkali waste liquid | |
Circulated Washing | *None since it is circulated | |
Electroless Cu | Electroless Cu | Heavy-metal acid waste liquid (contains Cu) |
Washing | Alkali waste liquid(weak) | |
Rust prevention | Waste water | |
Circulate Washing | *None since it is circulated | |
Drying |
Our contribution to the Sustainable Development goals (SDGs)
Our proprietary Pure Additive™ production technology has enabled us to produce printed circuit boards with less water consumption, hazardous byproducts, and carbon dioxide emissions than conventional production methods.
These achievements equate to a significant contribution to targets 6.3 and 6.4 of SDG 6, targets 12.2 and 12.5 of SDG 12, and SDG 13.
SDG Goal 6: Ensure availability and sustainable management of water and sanitation for all
Target 6.3 By 2030, improve water quality by reducing pollution, eliminating dumping and minimizing release of hazardous chemicals and materials, halving the proportion of untreated wastewater and substantially increasing recycling and safe reuse globally.Target 6.4 By 2030, substantially increase water-use efficiency across all sectors and ensure sustainable withdrawals and supply of freshwater to address water scarcity and substantially reduce the number of people suffering from water scarcity.
Goal 12. Ensure sustainable production and consumption patterns
Target 12.2 By 2030, achieve the sustainable management and efficient use of natural resources.Target 12.5 By 2030, substantially reduce waste generation through prevention, reduction, recycling and reuse.