Materials
The innovative materials behind our proprietary manufacturing process have all been researched and developed in house.
Nano ink
The nano ink used in our Pure Additive™ production process is composed of dispersed metal nanoparticles. Inkjet printheads are used to eject this nano ink and apply it to the substrate during the print patterning process. The layer of printed nano ink is then photosintered—a curing process that causes the metal nanoparticles to absorb light energy, causing them to heat up and melt together. This is the point at which the layer of metal nanoparticles adheres to the substrate.
Nano ink plays a crucial role in our Pure Additive™ production process and these inks are therefore developed to the highest standard to ensure they have all the properties required for use in printed electronics: they are a stable liquid that is dispersible via inkjet printheads, suitable for patterning, contain dryable solvent and curable nanoparticles, and can form a strong bond with the substrate on which they are printed.
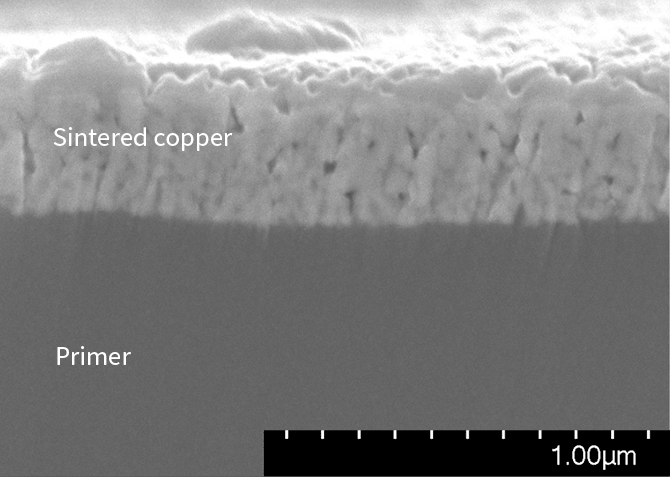
Primer
Primers improve adhesion between the nano ink and substrate. Using a primer creates a firm physical bond between the nano ink and substrate to ensure high adhesion of conductors in the circuit board. The time-consuming nature of conventional nano ink sintering methods used in printed electronics has been a major contributor to poor productivity in printed electronics mass production thus far. Now, with our primer and nano ink material design technologies, we can achieve the same adhesion in less than a tenth of previous processing times.
Our unique primer also helps control the behavior of ink droplets as they are dispersed during the inkjet printing process, making it an important contributor to effective patterning of more intricate wiring patterns.Additionally, while conventional printed electronics technologies required certain printing equipment specifications and print processing conditions, advancements in primer technologies have made it significantly easier to develop printing equipment and print processing methods that ensure high-definition and high-speed production without these restrictions.
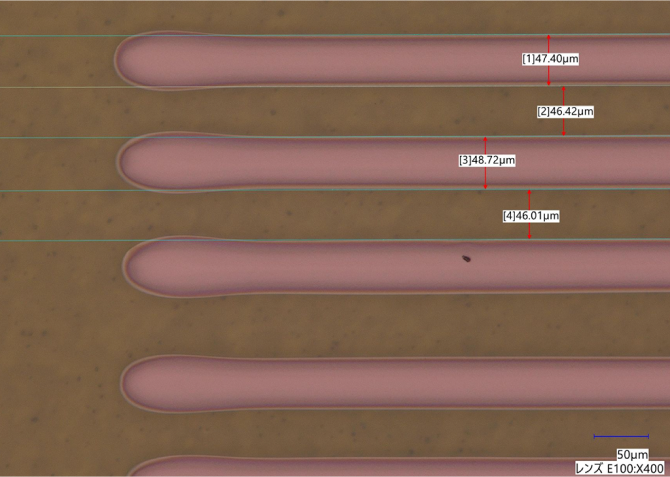
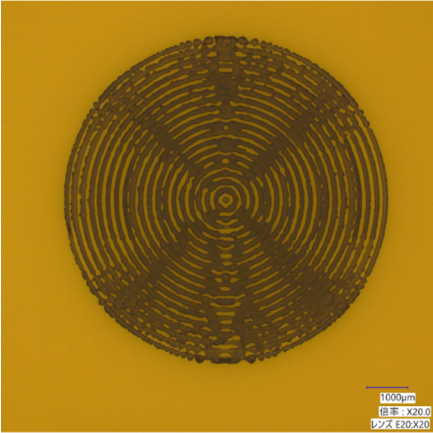
without droplet behavior control
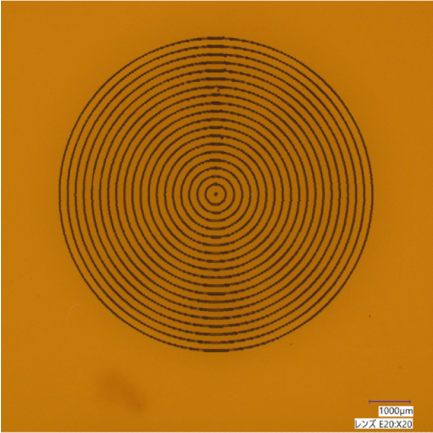
through droplet behavior control
Material analysis
Development of our cutting-edge materials was made possible through consistent implementation of phenomenon analysis technologies throughout the entire research and development process.For example, when working to achieve high adhesion between our nano ink and the substrate, we observed the behavior of individual metal nanoparticles and asked questions such as “why is adhesion strength decreasing?” and “what could be causing this loss of adhesion?” to determine the root cause.
At Elephantech, we believe that reliable, nano level control of materials and the phenomena they cause is essential to ensure the effectiveness of each step in our Pure Additive™ production process and using nano level analysis technologies enables us to identify critical issues and develop and implement countermeasures quickly and effectively.
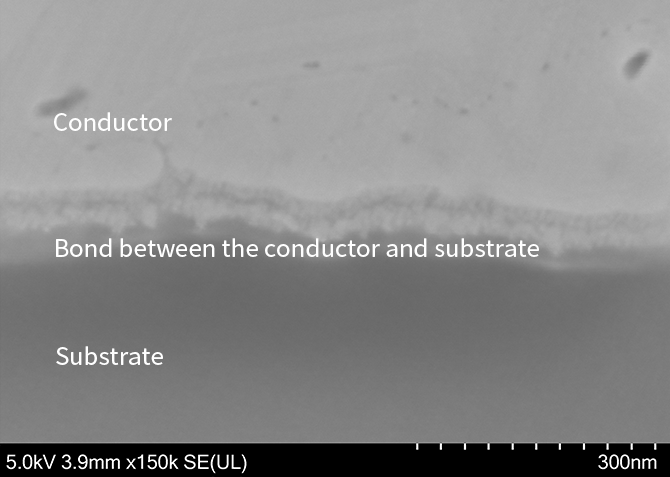
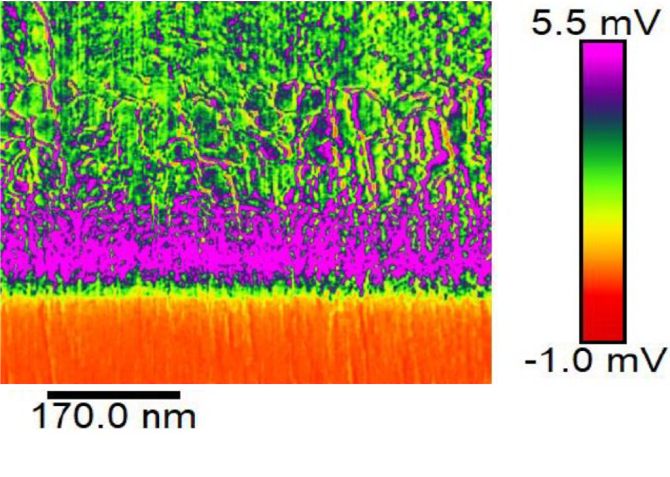
Determining the atomic state between the substrate and conductor